Does AD pay off on smaller farms?
Despite a reduction in government support, on-site plants can still offer advantages to smaller farmers, say industry experts.
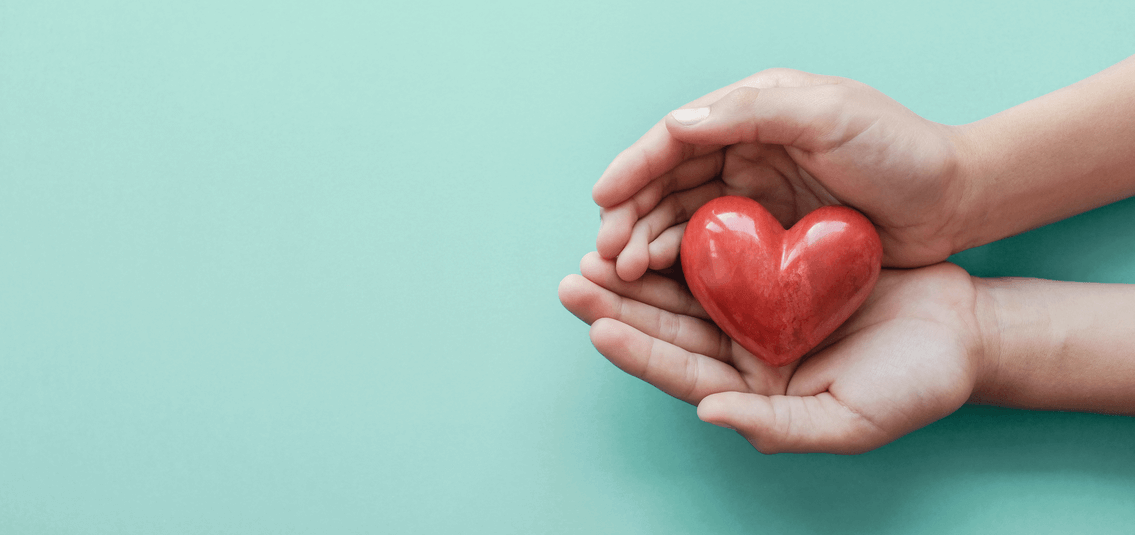
Despite a reduction in government support, on-site plants can still offer advantages to smaller farmers, say industry experts.
This material is published by NatWest Group plc (“NatWest Group”), for information purposes only and should not be regarded as providing any specific advice. Recipients should make their own independent evaluation of this information and no action should be taken, solely relying on it. This material should not be reproduced or disclosed without our consent. It is not intended for distribution in any jurisdiction in which this would be prohibited. Whilst this information is believed to be reliable, it has not been independently verified by NatWest Group and NatWest Group makes no representation or warranty (express or implied) of any kind, as regards the accuracy or completeness of this information, nor does it accept any responsibility or liability for any loss or damage arising in any way from any use made of or reliance placed on, this information. Unless otherwise stated, any views, forecasts, or estimates are solely those of NatWest Group, as of this date and are subject to change without notice. Copyright © NatWest Group. All rights reserved.